#TAd-Week
With Technical Attendant dictionary week, I will summarize conclusions and draw similarities between small and full-scale racing. Everything written is either based on my experience or general knowledge. It is simplified; in detail, it is much more complex. It will only provide a general understanding of technical topic. Car settings depend on various factors like track specifications, track conditions, and driver preferences.
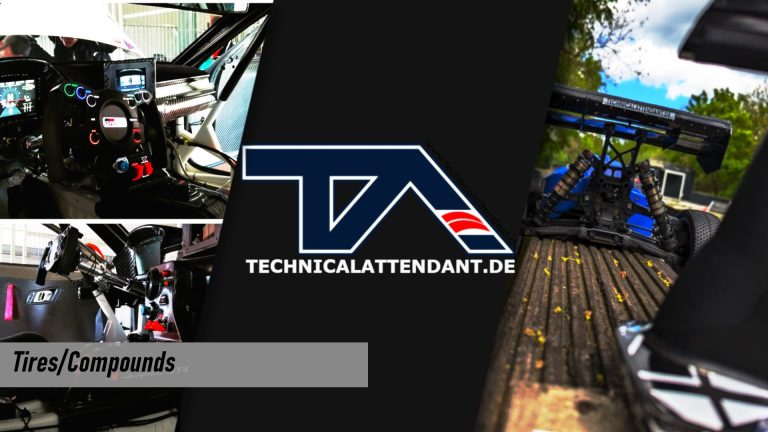
One of the most important components on a race or road car is the tire. Why? Because, in the best-case scenario, the tire is the only part directly in contact with the surface of the racetrack. In the worst case, it might be the roof or other parts of the car.
Every force and all feedback regarding steering, braking, and acceleration are transmitted through the tire. That's why it's crucial to pick the right tire and understand its behavior throughout a race.
The corners of the car are always a critical area to develop. Corners include not just the suspension, but also the brakes, tires, and rims. In road-based race car development, this area is especially tricky because the room for changes is limited by space or regulations. In customer motorsport, such as GT3 or GT4, you also want to avoid using expensive, machined parts. That’s because, especially the brake cooling system, is highly vulnerable during frontal impacts, which could negatively affect a customer’s budget.
Additionally, GT3 and GT4 cars have gotten heavier and larger over the years, which leads to increased thermal challenges in this area.
Tire Data
Important data is collected via telemetry, sensors, etc. Key values include:
- Tire pressure (TPMS)
- Tire temperature (inner, middle, outer)
- Tire loads
- Lateral forces
- Slip ratio and slip angle
- Acceleration values
Why are these data points important and what do we do with them?
The contact patch (the area in direct contact with the track) gives us insight. For example, looking at tire temperature data across the inner, middle, and outer sections can reveal setup issues, like camber, incorrect tire pressures, or toe settings.
The running tread of a tire will also offer clues about whether adjustments are needed. You can even observe how tire behavior changes over several laps, indicating under- or overloading. This becomes particularly important in series where teams are not allowed to preheat tires. When cars leave the pits cold, drivers struggle to find grip until the tires warm up.
Getting the tire to its target temperature depends on:
- Suspension design
- Center of gravity
- Roll center
- Components like dampers
- Driving style
Cold and warm tire pressures are key indicators of both setup and performance. Lateral and longitudinal forces (visible in data analysis tools) provide insights into traction, braking performance, and tire wear.
Below is a picture of a worn tire, which probably has a bit too much camber as you can see graining on the inner side of the tire.
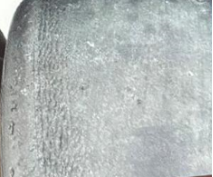
Common tire issues are:
- Overheating -> Pressure rises, one area shows high temperature.
- Graining -> Less grip but stable temperature (picture below)
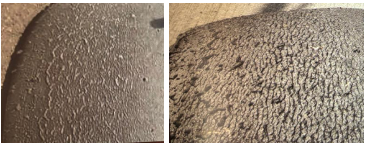
- Blistering -> Sudden performance drop, pressure drop
- Wrong camber -> Bir temperature difference inside vs outside
- Low pressure -> Slow heating, spongy feeling (example below)
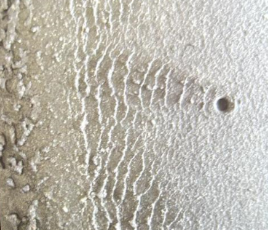
- High pressure -> Center of tires is hotter than outside
The maximum grip a tire can generate is illustrated by the traction circle. The radius changes continuously depending on:
- Tire wear
- Temperature
- Track conditions
Below is an example of a traction circle:
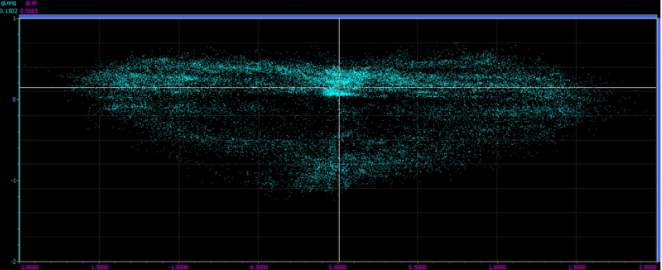
The radius of the traction circle can vary continuously throughout the day due to tire wear, temperature, or track surface conditions.
Below is an example of a traction circle. The top of the circle may appear chopped off, which is typical for most circuit race cars that have only two driven wheels (either front or rear). In such cases, the car will generate force only during acceleration, and must also overcome aerodynamic drag. Under braking, however, all four tires contribute to deceleration.
There can also be a difference in lateral force between the left and right sides of the car. This can result from an asymmetrical setup, or due to track-specific factors, such as corner banking.
The maximum grip a tire can produce also depends on the vertical load applied to it.
A key factor here is the slip angle—the angle between the direction the tire is pointing and the direction it is actually traveling. This difference in angle generates the lateral force that allows the car to turn.
Each tire has a characteristic slip angle curve, which indicates the optimal slip angle at which the tire generates the maximum lateral force.
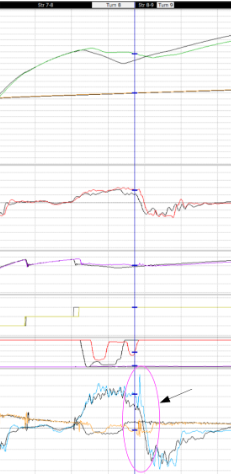
The picture above shows two overlaid laps. The blue graph in the highlighted area (marked by an arrow) illustrates a situation where the car lost grip. This is indicated by the sharp peak in the blue trace. In addition to the peak, the other graphs also suggest that something unusual occurred, but we won’t go into those details here.
This size of the traction circle is not constant. Under high downforce conditions, the diameter of the circle is larger compared to low-speed sections.
The area with the highest density of data points gives you an idea of whether the car spent more time accelerating or braking.
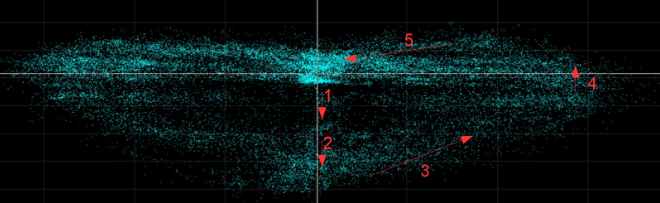
Traction Circle Phases – Lateral and Longitudinal Forces
- Position 1: The car is approaching on a straight. Since there are no lateral forces, and the car is at or near top speed, the G-forces gradually decrease.
- Position 2: The negative G-forces increase as the car begins braking into the corner. In a straight-line braking zone, all available grip is used for deceleration. For high downforce cars, this slope will decrease even further as aerodynamic forces diminish with reduced speed.
- Position 3: This phase represents trail braking. The driver begins releasing the brake while starting to steer into the corner. At this point, maximum grip is shared between braking and steering. In theory, the data trace should follow the edge of the traction circle, using all available grip. However, real-world behavior rarely matches theory due to many variables.
- Position 4: Here, the car reaches the apex of the corner. All available grip is now dedicated to cornering. After the apex, the driver begins to apply throttle, and longitudinal G-forces start to climb back above zero.
- Position 5: In this stage, steering input decreases and more grip becomes available for acceleration. Maximum acceleration is achieved once the engine power cannot break traction and the throttle can be fully applied.
Let us have a look at the tire temperature evolution across laps because this is also a very complex and interesting topic
Tire temperature development must be considered across different components:
- Tire surface temperature
- Rim temperature
- Brake disc heat, which transfers into the rim and tire
Lap 1 (Cold Conditions)
At the start of the stint, both tires and brakes are cold. Heat transfer begins immediately during the first heavy braking—for instance, a corner requiring a downshift from gear 6 to 2.
When the driver presses the brake pedal, heat from the brake disc begins to transfer into the rim and tire. However, the system hasn’t yet stored much thermal energy.
Throughout the braking, cornering, and acceleration phases, tire surface temperature builds through friction. However, the system cools down quickly again—brakes are not yet fully efficient, and grip levels remain low in these early corners.
Lap 5 (Stable Thermal State)
By lap 5, the entire system is significantly hotter. The tires, rims, and brake components retain heat, and cooling is slower.
- Inner tire temperature rises due to sustained friction energy.
- Inner temps don’t fluctuate as quickly as outer temps, since airflow cools the tire exterior more effectively.
- After several laps, rim and inner tire temperatures stabilize in the same general range.
Inner temperature readings can also indicate whether camber settings need adjusting. In addition, the temperature distribution across the tire helps you evaluate how the pressure distribution is behaving.
A slow temperature rise also correlates to a slower pressure increase, which is crucial for predicting tire behavior over a stint.
Key points to take away:
- Internal tire temperature increases consistently until it reaches a stable plateau.
- Rim temperature follows a similar trend to the inner tire temp.
- Surface and rim temps can fluctuate more dramatically but still follow a predictable pattern lap to lap.
A slower lap often shows reduced temperature build-up, visible in less dramatic temp distribution.
RC Tires
There are many different RC tires available, but for the purpose of this article, I’ll focus specifically on the 1/8 scale tires I use and provide only general information.
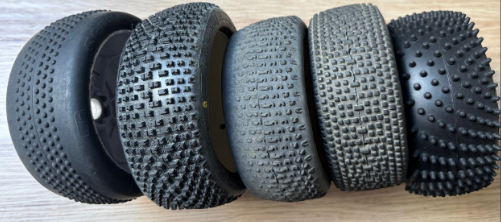
An RC tire consists of three main components you see in the picture below:
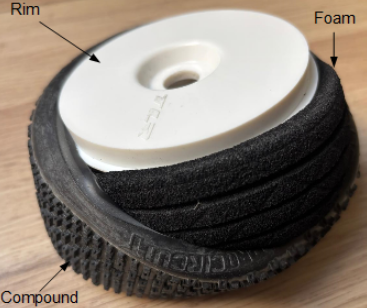
The tread profile is the most important factor and needs to match the track surface. While I won’t go into full detail here, it’s worth noting that there are many different tread patterns to choose from. However, in some racing series, tire choices are restricted by regulations.
For the tires we use, we have several tread profiles and a variety of compounds, ranging from super soft to soft and hard.
The performance difference between these compounds is even more significant than I initially expected.
Foam Selection in RC Tires
Besides having the correct width to fit inside the rim and tire, the stiffness of the foam insert is equally important.
A stiffer foam helps reduce tire deformation under heavy loads. This is especially important at high speeds, where consistent performance and predictable handling are key, since the contact patch—or “latch”—remains more stable.
On the other hand, softer foam allows for more deformation. While this can lead to an unstable or imprecise feel under heavy loads, it can be beneficial on bumpy tracks. Softer foam increases the contact patch, enhancing grip where the surface is uneven. However, if the foam is too soft, it may cause the car to feel unsettled or inconsistent during fast driving.
It’s fair to say that foam stiffness in RC cars is somewhat equivalent to tire pressure in full-scale racing. Unlike full-scale cars, you won’t get a puncture in RC racing, but there is a risk of the glue coming loose. If that happens, centrifugal forces can cause the foam to be ejected from the tire, leading to failure.
Conclusion
The tire and its compound are among the most critical components of any car, whether RC or full-scale racing.
As always, this topic is highly complex, with far more opportunities for data analysis and tire behavior observation in full-scale motorsport.
While tire performance depends heavily on the manufacturer, RC racing gives you more flexibility in selecting the right tire profile for specific track conditions.
In both RC and full-scale racing, tire wear provides valuable feedback on whether your setup is optimal or requires adjustment.

When I decided to participate in races, I knew I had to approach RC racing a bit differently. Having fun remains the highest priority, but I also wanted to achieve good results. To do that, you need to improve your lap times through better driving. Whether in RC or full-scale racing, finishing in good positions requires fast and consistent lap times. If your average lap time is slow, you won’t secure top spots.
Both the driver and the car must adapt to the dynamic circumstances of a race. Factors like tire wear, traffic, and changing track surfaces are just a few of the variables that can change a car’s behavior. Good drivers can adapt to these changing conditions while maintaining consistent lap times. This requires a strong feel for the car something Germans often call the "Popometer" (a humorous term for sensing a car’s behavior through your seat).
The biggest question for me was: What do I want from the car? The answer seems simple "I want the car to be predictable." But what does that really mean? How much oversteer is acceptable? Do I want more off-power steering or on-power steering? These were just a few of the many questions I had, with very few immediate answers.
In full-scale racing, data logging is often used to improve lap times. This powerful tool not only helps monitor the car’s vital functions but also identifies where and why a driver is losing time.
To give you a better understanding of how data logging supports engineers, mechanics, and drivers, let’s take a brief detour into its application.
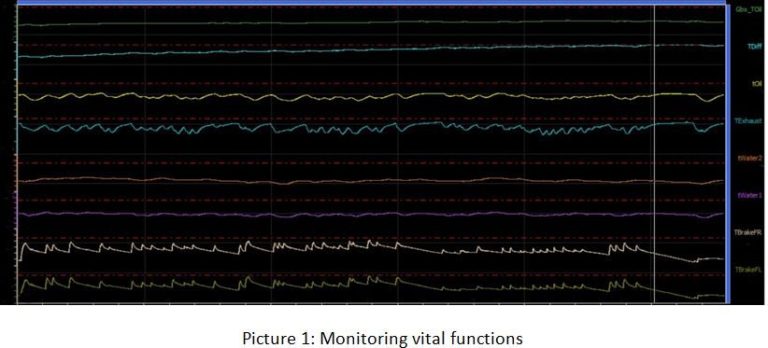
Picture 1: Monitoring Vital Functions
Picture 1 provides a quick overview of the car's vital functions, focusing primarily on temperatures. The red dotted horizontal line represents the maximum allowable values. For instance, you can clearly see that attention is needed for the differential temperature (T_diff). The graph shows a continuous rise, nearly reaching the red dotted line. Without intervention, this could lead to a race-ending issue.
To address this, you should investigate the root cause. Begin by checking the voltage of the differential pump. However, in this case, it’s unlikely to be a pump issue, as a non-functional pump would produce different temperature peaks. Instead, focus on the cooling system, such as inspecting the fresh air duct in front of the differential cooler. It’s also important to confirm with the driver whether they went off track into gravel, as gravel can damage the cooler’s entry depending on its placement.
From an engineer's perspective, you analyze the data through three primary roles:
- Monitoring Vital Functions: Ensuring the car is operating safely and reliably.
- Adapting and Tuning the Setup: Optimizing the car for the current conditions.
- Supporting the Driver: Identifying areas where the driver can improve lap times.
These roles are interconnected, and priorities often shift depending on the situation. Usually, the first priority is ensuring the car is running smoothly. This involves checking all temperatures, pressures, and voltages.
Speed Channel: Insights for Driver Improvement
The speed channel is one of the most critical data points for driver and car performance. It provides valuable insights into cornering behavior, braking points and effort, wheel lock-up, traction levels, aerodynamic efficiency, and more.
Performance and Setup Optimization
For setup tuning and performance enhancement, driver feedback is key. By overlaying data, you can identify opportunities to improve both the car and the driver’s performance.
For instance, picture 2 shows some key graphs you want to check to improve the driver performance.
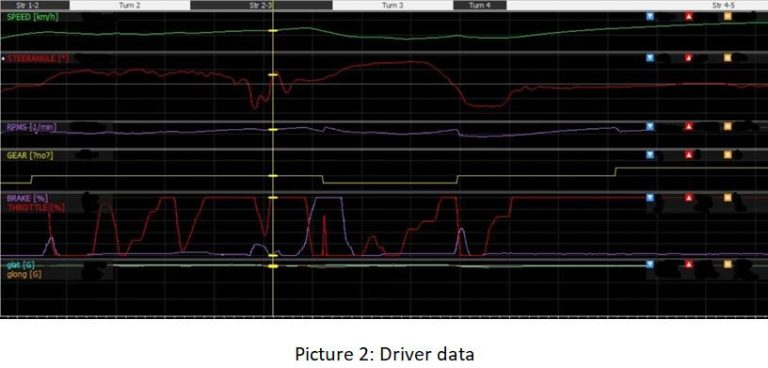
Picture 3 is highlighting this area. This conclusion can be further validated by having a closer look to the G-force values and wheel speed data.
Finally, it’s essential to align these observations with the driver’s feedback, as they have firsthand knowledge of what happened during that moment.
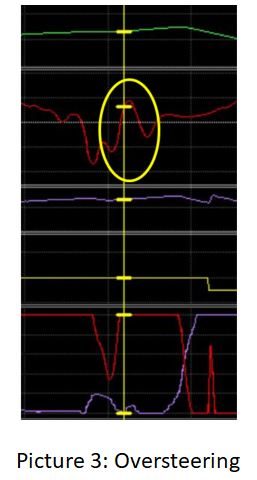
Picture 4 shows an overlap of two laps. In the top graph, the red line indicates the lap where time was lost. In yellow highlighted area, you can see that the engine RPMs and speed graph for the red line drop slightly earlier than for the green line. This suggests that the driver of the red line braked and shifted down earlier, resulting in the time loss.
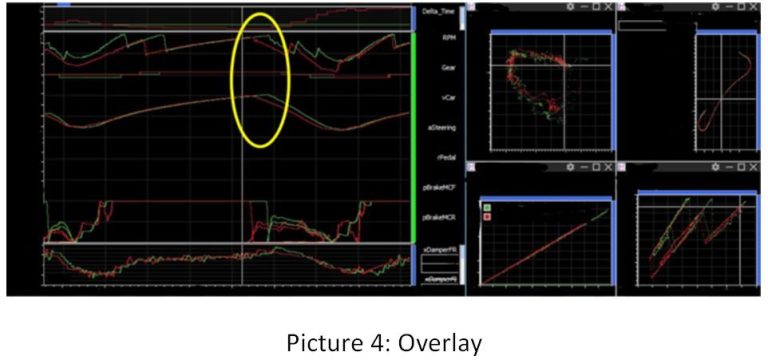
There are countless ways to analyze data in full-scale racing. Unfortunately, these tools are not as common in RC racing. I found myself struggling to figure out where to start, even though there was (and still is) plenty of room for improvement. 😊
In RC racing, you don't experience the car directly as you would in full-scale racing. Instead, you give commands via a remote and observe the car's behavior, which I would describe as an indirect feedback. Over time, you develop a sense for what the car does when you pull the throttle or steer, but this can vary significantly depending on the track surface. Initially, I found it incredibly challenging to understand how the car should feel and what direction to take with the setup.
It wasn’t until I drove my friend's car that I started to understand what a well-set-up car should feel like. His car handled bumps more smoothly and was much less nervous when braking into corners, whether on or off throttle. In general, his car invited me to push harder, while mine felt like it was constantly asking me to slow down. Combine this with my lack of skill at the remote, it was difficult to achieve consistent “fast” lap times.
This experience marked the first time I began to understand what it means for a car to feel predictable. It also gave me a clearer idea of what I needed to work towards in terms of setup.
The main takeaway here is that understanding the car behavior isn’t always straightforward. It requires experience not only with the car on the track but also in observing its behavior and drawing the right conclusions. After a few adjustments, my car started to feel better, but there was still significant room for improvement.
My breakthrough came when my friend Nico observed my car and pointed out that the front axle seemed to be “pulling” the rear axle, causing the car to feel nervous. With this advice, I made a few adjustments and was finally able to balance the car better. This underscores a crucial skill in RC racing:
Observing your car and making the correct adjustments based on what you see.
Of course, the biggest factor is still practice and time spent at the track. About 70% of my issues were due to the person holding the remote. But the other important piece is understanding the car’s behavior and knowing where you want to take it. Learning to observe and draw the right conclusions is just as essential as improving driving technique.
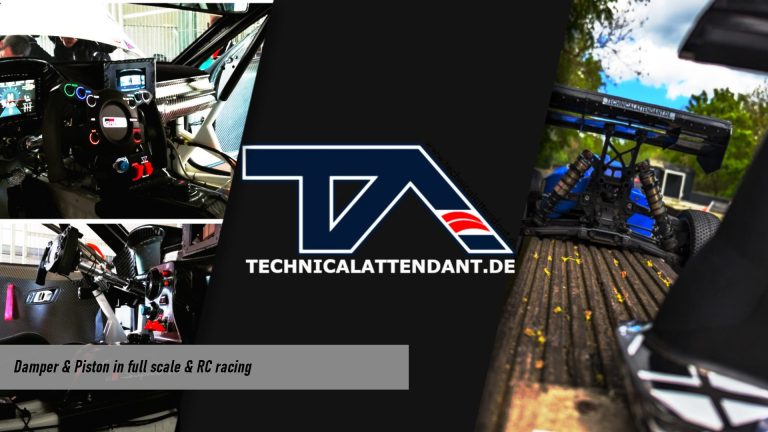
Dampers and springs are a science in themselves, and they’re a topic that can lead to endless discussions, whether in RC or full-scale racing. This topic is always a hot one but also not an easy one. Choosing the right setup requires an understanding of suspension theory, vehicle physics, and the driver’s needs. Getting it right can significantly improve the car's performance, but the wrong setup can make things worse.
In my last article, I already covered one part of the suspension assembly, and now it's time to dive into the next component. I will again try to compare RC Racing with my experience in full scale racing.
The last race was in Oberhausen, a track with loose, bumpy ground. It was a great opportunity to explore damper oil and piston specifications in detail. Generally, on bumpy tracks, you’ll want to soften the springs and/or choose oil with lower viscosity, but there are also other adjustments you can make to improve handling.
Let's start with some basics and go over key terms.
What are Shocks?
Also called dampers, shocks serve to control and reduce the movement of springs. They also influence handling, especially during cornering. Most performance vehicles have four shocks, typically oil-filled, with adjustable pistons, springs, and suspension travel.
In Illustration 1, you can see the main parts of an RC damper. While there are also additional components, such as nuts and sealing rings, the primary parts are shown here
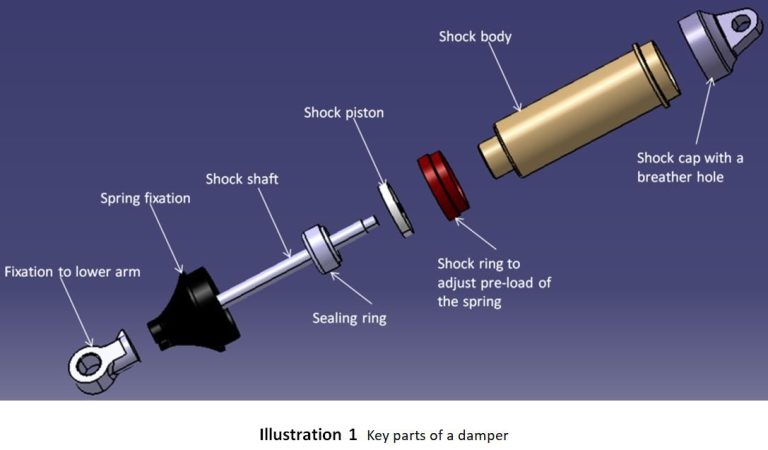
In preparation for the race, I focused on gaining a better understanding of selecting the right piston. In 1/8 scale racing, pistons typically have 5 to 8 holes, with diameters ranging from 1.2 to 1.5 mm. While there are pistons with up to 20 holes, for this article, we’ll concentrate on those with fewer holes. In illustration 2 you see some examples.
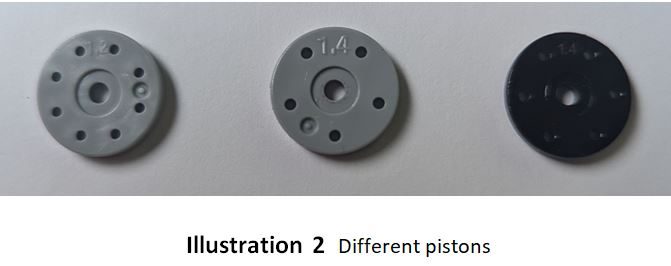
The piston is fixed to the piston shaft and moves up and down through the oil within the shock body.
The Pack:
Pack refers to the force created when the piston moves up and down at high frequency. This movement generates resistance in the damping process, which affects the car's handling behavior.
So, where does this resistance force come from? The root cause is a condition called “shear stress.” To understand this, we’ll start with the concept of the boundary layer.
Boundary Layer:
When air or fluid flows near a surface, its velocity at the surface is zero due to the “no-slip condition.” The fluid particles directly in contact with the surface have no relative velocity. However, as you move further away from the surface, the velocity gradually increases until it matches the free-stream velocity at a certain distance.
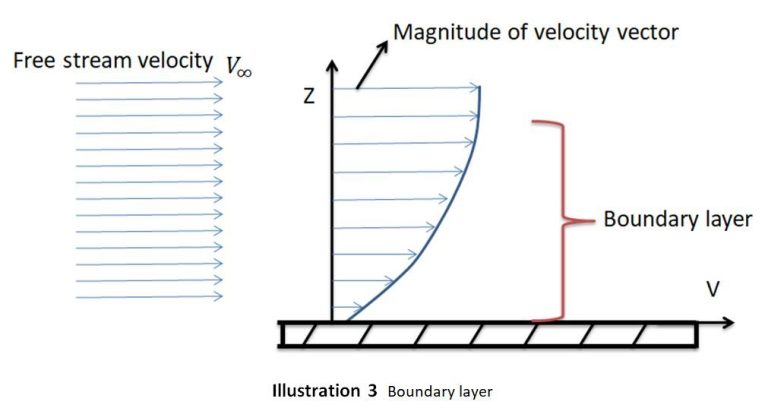
The boundary layer (illustration 3) forms wherever air or fluid is in contact with a surface. Variations in velocity within this boundary layer affect shear stress, which in turn creates resistance in the damping movement. Shear stress is defined by the formula:

where:
∂v/∂x = rate of change in velocity relative to distance from the surface
According to this formula, shear stress—or resistance force—is influenced by the fluid's viscosity (μ) and the velocity of the piston's movement (v).
When considering the area around piston holes, velocity distribution is impacted by hole size. This variation in velocity distribution across different hole sizes directly affects the damping characteristics.
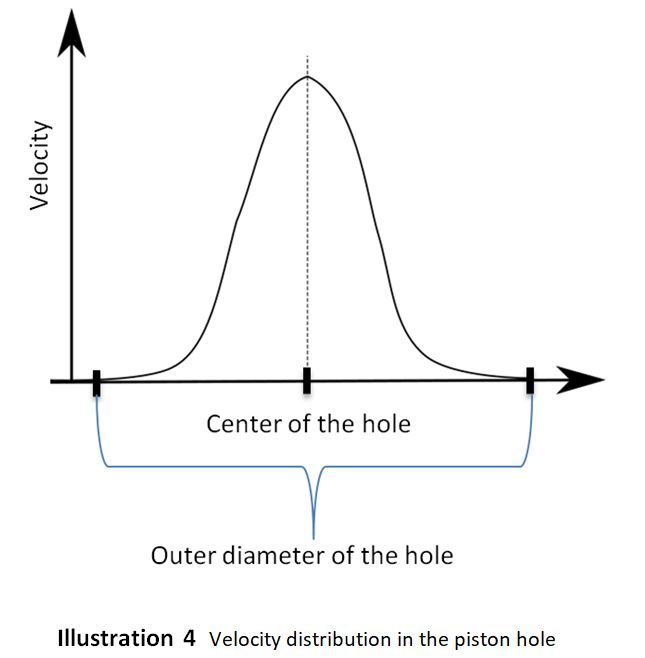
This means that fluid velocity is highest at the center of the piston hole, and as the frequency of piston movement increases, so does resistance. The amount of "pack" (or resistance) can be influenced by the viscosity of the oil used in the damper.
So, what does this mean, and how can we use it to choose the right oil and piston for different conditions?
Generally, low-speed damping occurs when the damper moves slowly, such as during cornering when the chassis rolls. On a smooth, high-traction track, you have minimal suspension travel. However, high-speed damping can occur when landing from a jump, as the damper absorbs the impact quickly.
High-speed damping happens on a bumpy track, where the damper moves rapidly to absorb frequent impacts, or when landing from jumps.
If you increase the size of the piston holes while keeping the same number of holes, low-speed damping becomes softer, but high-speed damping (pack) increases as well.
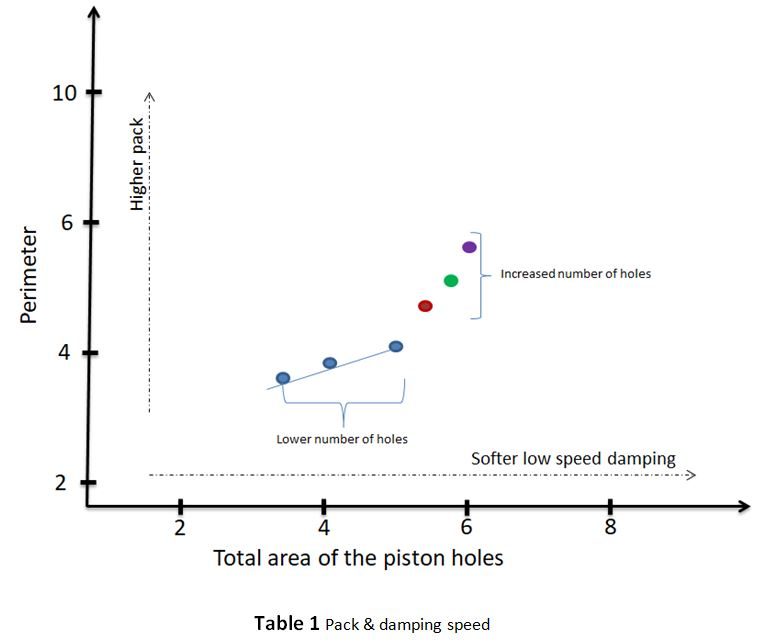
Looking at the table above, we can derive the following:
- To achieve similar low-speed damping with higher pack, you would select piston plates with a greater number of smaller-diameter holes.
- On a bumpy track with increased suspension travel, you’ll want to reduce pack so the damper can absorb more energy. For this, choose pistons with fewer, larger-diameter holes.
So, all of this is the theory which I use as a guide line, surely it can vary depending on driver preference or track conditions.
Full-Scale Racing:
Applying these principles to full-scale racing is challenging, as the topic is far more complex. I’ll provide a brief overview specific to GT racing, as settings for formula or prototype cars differ substantially, often taking an entirely different approach. This is just a glimpse into the complexities of damper setup, which depends on numerous factors.
During development, collaboration with damper suppliers is essential. Their expertise is crucial to achieving optimal damper settings. In GT racing, cars face a wide variety of tracks, drivers, and applications. GT3 and GT4 cars compete worldwide, so they need to perform well for both professional and amateur drivers. This is a major focus during development since pro drivers have a very different feel for the car compared to amateur drivers, yet both must be able to drive it to its limits. In many series, driver changes are common, so the setup must suit both drivers’ needs. Tire variations add another layer, as different manufacturers affect grip and wear characteristics.
All of this means that damper settings need to cover a broad range to maximize performance. Each GT car has unique characteristics based on factors like weight distribution, center of gravity, and roll center height, all of which are crucial considerations in development. Solutions are found through simulations, 7-poster rig tests, and extensive testing on various track layouts. Strong teamwork and partnerships are essential to address every aspect.
Another critical aspect is design. Mechanics must be able to access dampers easily, but this can be restricted by regulations. GT2, GT3, and GT4 cars are based on production models, so modifications are limited to stay within regulations. For instance, the wishbone pivot points can only be modified in a certain range. Manufacturers also aim to minimize modifications to keep costs reasonable for the market, balancing affordability with performance.
This complexity is a big part of why I’m passionate about customer racing, as it combines competitive car setup, cost management, after-sales support, and customer satisfaction a challenge that is often underestimated.
The Role of Data and Engineering in Damper Setup:
In full-scale racing, tools like data logging and effective driver-engineer communication are critical to optimizing damper settings. Driver feedback is vital for efficient setup changes, but how does an engineer know what adjustments to make?
Experience is invaluable, but data logging also plays a significant role. Racing cars are equipped with various sensors some required for Balance of Performance (BoP), others to monitor vital functions like temperature and pressure, and others specifically for damper data.
Below is a snapshot from a data recording system in a circuit racing car. It provides insights into suspension travel, damper velocity, and individual wheel speeds.
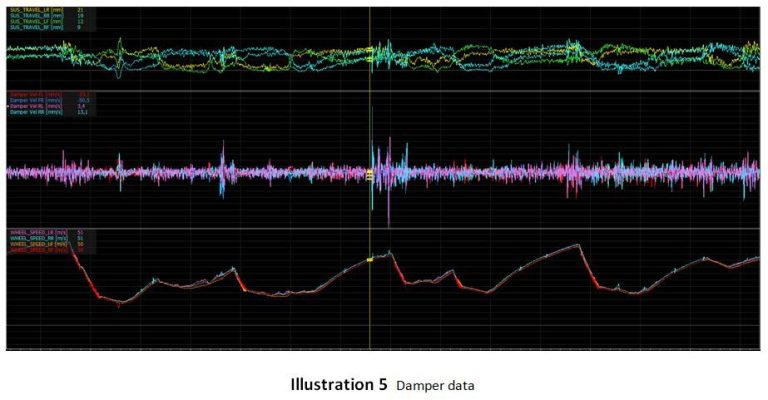
By reducing the number of channels and zooming in on the front left damper traces, we can isolate and analyze damper travel during compression and extension, as well as damper speed.
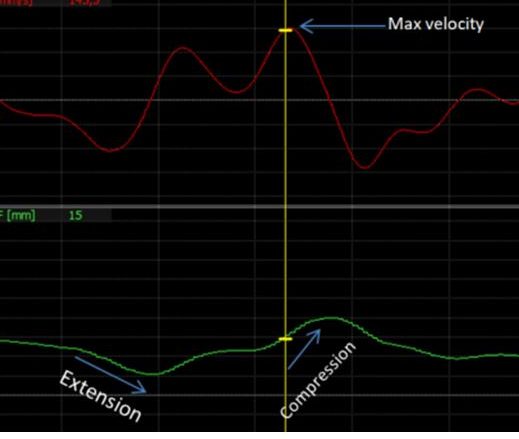
Beyond the actual data, examining the duration between compression and extension can provide insights into damper settings for rebound and bump. However, this analysis must be approached carefully, as track surface conditions can also affect damper behavior. For instance, high damper speeds can result from a bumpy surface or cornering over curbs, similar to high-speed damping in RC racing when landing a jump.
Damper activity data can also be used to calculate the car's chassis roll, helping identify how the car behaves through corners. By analyzing damper traces, you can observe the car’s behavior during the four main stages of cornering:
- Braking into the corner
- Initial cornering
- Apex cornering with initial throttle application
- Corner exit
This detailed analysis allows for in-depth comparisons between drivers and fine-tuning of damping settings. Another valuable tool for evaluating damping setups is the damper shock speed histogram, which offers further insights into damper performance.
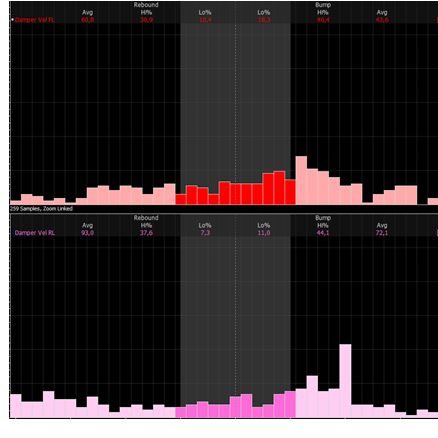
This histogram illustrates the damper speed ranges for low- and high-speed damping. Low speeds, generally up to 25 mm/s, typically reflect chassis roll, while speeds above 200 mm/s are reached when taking curbs in corners. Generally speaking, for optimal performance, the goal is a speed histogram that is as symmetrical as possible.
Conclusion:
In full-scale racing, you have far more tools and data to analyze damping behavior, and the process is indeed more complex. However, the foundational principles are the same. By applying the basics of low- and high-speed damping, you can enhance car performance not only in RC racing but also in full-scale racing.
Starting on the Topic: ARB and Getting Lost in BoP
What is an Anti-Roll Bar?
Anti-Roll Bars (ARB), also known as Sway Bars, are used to control chassis roll while cornering by connecting the left side of the car to the right side. In RC racing, it is a fixed diameter bent piece of wire that is attached to the differential box and suspension arms via links.
Why Do Cars Need an ARB?
During cornering, the car starts to roll toward the outside tires (e.g., in a left-hand corner, the car rolls towards the right-hand side tires in the direction of travel). This rolling causes a load change on all four tires, and with the load change, you will have different grip levels on each tire. One of the objectives in racing is to be fast, and to be fast through corners, you want to have a good grip level on all four tires. The ARB is one part of the suspension system that helps to equalize the load on the tires.
What Does the ARB Actually Do?
When the car is cornering, the chassis rolls first, and then the load is transferred to the outer tires. This means that the load transfer is delayed because the car initially puts energy into the damper/spring system. The ARB, depending on its specification, creates torsional resistance to control the roll of the chassis and to keep as much of the tire surface as possible on the ground. Tires, track surface, dampers, springs, etc., all influence each other and surely impact the effectiveness of the ARB.
To get a better idea of this topic, please have a look at the video on my Instagramm account:
https://www.instagram.com/technical_attendant/
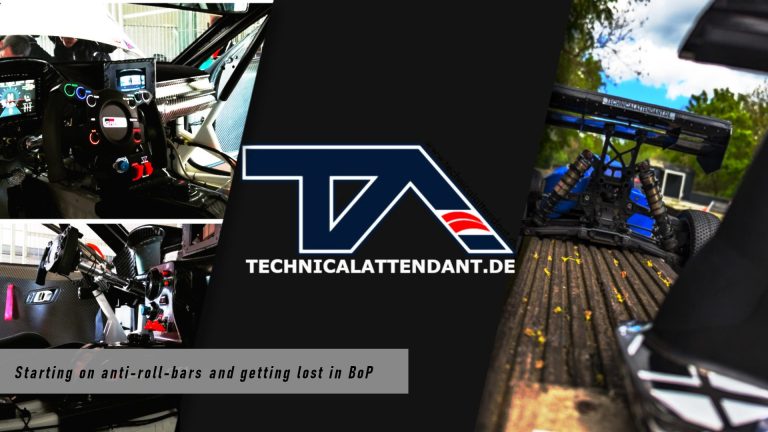
To make things even more complicated, cars have an ARB at both the front and rear, and through the chassis, everything you do at the front impacts the rear—but in the opposite way.
You always try to achieve a good balance in the car because this makes the car predictable—predictable in terms of avoiding any unexpected movement, such as sudden oversteer or understeer in corners. If the difference between the front and rear ARB is too big, this can cause unpredictable car behavior. On a high-grip track, the forces on the car are higher, and the car will pitch and roll more. Depending on what you want to achieve, you may opt for a thicker or thinner ARB. Usually, when you are on a low-grip or wet track, you want the car to roll more, so you choose a thinner ARB.
In full-scale racing, all of this is a bit more complex and depends on the car's specifications. A GT race car (GT3, GT4, etc.) has a completely different suspension design than a Formula or Le Mans Prototype car. Usually, in GT racing, the ARB is a large torsional spring shaped in a U-form. The middle is attached to the subframe, and the ends of the ARB are connected via ARB links to the strut assembly. Formula and Prototype cars usually have a system of rockers, pushrods, heave springs, etc., but I won’t go into more detail as this would go beyond the scope of the topic. There are more suspension systems, but those used for GT and Prototype cars are the most common ones.
Generally, all cars must follow regulations, and their design must be homologated by the FIA, ACO, SRO, or other governing bodies. In GT racing, the parts are homologated during an inspection where a representative of the governing body visits your factory to check that the actual parts comply with the series regulations. For the inspection, you also need to prepare the homologation form, which documents the car's design. This form serves as the reference for all races during technical scrutineering at events. Along with the car's specifications, the governing body also conducts simulations to define the BoP (Balance of Performance).
BoP? What Is the Balance of Performance?
Since I have mainly been involved in GT racing in my career, I will focus on GT cars. In GT series like GT3 or GT4, you have different manufacturers and a big variance in powertrain (engine sizes, etc.) and chassis specifications (location of center of gravity, roll center, etc.). To equalize the chances for each concept, the performance of the cars is adapted by adjusting ride height, engine power, and weight. The BoP is defined at the beginning of the season but can also be adapted before and during each race. As the characteristics of cars from different manufacturers can be very different, performance can vary depending on the track layout. A car that works well on tight tracks may not perform as well on a wide track with lots of straights.
Teams also have to provide data so that officials can compare the performance of the cars. The governing body defines which data channels (RPM, speed, throttle position, etc.) must be recorded and provided. This is not only to control the car's performance but also that of the driver. Not saying that anyone does it ;-) but teams could complain about a bad BoP because the car has too much weight or needs more power, while in reality, the driver is “unintentionally” not using the car's full potential. In this case, the officials can check the data and compare it with other cars from the same manufacturer.
There are a lot of discussions and complaints regarding BoP specifications, and in my career, I’ve been on both sides—the manufacturer side and the BoP specification side. I have to say, defining the BoP is not an easy job because there are so many factors that impact it. Driver skills, car performance, and even political aspects all come into play because manufacturers want their teams to win. In the end, GT customer racing is a business, and manufacturers want to sell cars. As a team, you want the best car because winning attracts sponsors and drivers.
Especially when it comes to customer racing and the dynamics between manufacturers, customers, and governing bodies, I could start writing and discussing endlessly. It's a fascinating and challenging area that, in my opinion, is often underestimated compared to factory racing (like F1, etc.).
I could write endless lines about this topic, but we’re already too far from the initial topic. :)
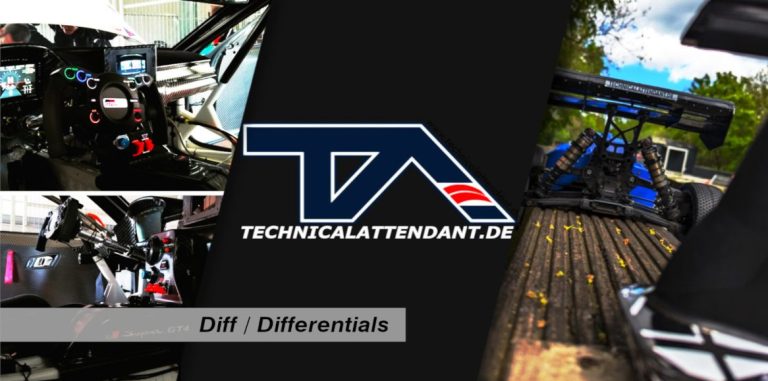
I have to admit that diffs and gearboxes have always been a mystery to me. I never fully understood how the mechanics work inside them. Even when experts explained it to me, I only understood it in that exact moment, thinking, “Ah yes, that’s pretty logical and not that complicated.” Thirty seconds later, my brain would say, “Computer says ‘no’” (a Little Britain reference), and it was all gone.
I decided to leave this to the experts because, for me, it was important to understand what a diff does and how to adjust it regarding performance and handling of the car.
In RC racing, you can change a differential in roughly 8 minutes, and you change the oil specification depending on the surface, tires, and conditions. So it was time to catch up on this topic. Luckily, 8th scale buggies don’t have a gearbox 😊.
8th Scale Racing:
In 1/8 scale buggy racing, you typically have three differentials: front, center, and rear. Inside the differential, you have gears and oil.
The front and rear diffs mainly influence the steering and rotation of the car, while the center diff controls most of the power and explosiveness. The differential at the front and rear allows the tires to turn at different speeds during cornering. This is important because, when driving around a corner, the inside tire has to follow a tighter arc than the outside tire due to the steering geometry. This means the tires cover different distances in the same period of time, so their speeds must be different.
The differential controls the power delivery to the tires, thus affecting the car's handling. This is crucial to understand when adjusting your car to different surfaces or conditions. You adjust this by using oil with different viscosities, which controls the resistance inside the diff. Viscosity describes how viscous a fluid is. For example, honey is more viscous than water.
As the diff controls the power supply, you have to distinguish between off power (throttle not pushed) and on power (throttle pushed). To simplify it even more, you could say:
- Off power -> approaching a corner, braking in the corner
- On power -> accelerating out of the corner
A general rule for choosing the correct oil is:
- Front: Thicker oil reduces steering, making the car less nervous. This works well on high-grip tracks. Thinner oil does the exact opposite.
- Center: Thicker oil will increase power delivery and explosiveness but is harder to drive. Thinner oil is easier to drive.
- Rear: Thinner oil will generate more rotation of the car, which is harder to drive. Thicker oil does the opposite.
The above is very simplified but gives a good idea of how the oil specification impacts the car's handling. How you set up your car depends on the driver, the track (high or low grip), the track conditions (dry or wet), and even the tire choice can have an influence.
Full Scale Racing:
Whether it is full scale or small scale racing, the differential works the same, but for each application, it is more complex or simple in its own way. The hardware is, of course, very different, as you have much higher forces in full scale racing. In small scale racing, for example, you won’t find differential cooling, whereas in full scale racing, it is a must. In full scale racing, there is a big variety in how the diff is built, but for this article, I will concentrate on limited slip differentials, as these are the ones I worked with most of the time.
In limited slip differentials, you can adjust the locking torque by changing different ramps, friction plates, oil viscosity, or preload.
Locking torque: As we already know, the diff allows the left and right tires to turn at different speeds. This also means you have differences in torque between the left and right tires. If the torque difference is lower than the locking torque inside the differential, the differential will be locked, and there will be no speed difference between the left and right tires. If the torque difference is higher than the locking torque, there will be a high speed difference between the left and right tires.
Adjusting locking torque: By increasing the locking torque, you decrease the speed difference. No locking torque means a high speed difference; high locking torque means no speed difference. The question is not low locking or high locking, but how much should it lock, how much should it decrease the speed difference.
If the preload is low, the outer tire is much slower than the inside tire, creating a backward force, while the inner tire creates a forward force, causing oversteer (rear breaks out, loses traction). In most cases, oversteer is worse than understeer.
A good way to remember this is:
- Oversteering: you don’t see the impact; you only hear and feel it (rear impact first).
- Understeering: you see the impact (car slides front-first into the barriers).
This is also what I experienced when I did development work on a GT3 and GT4 project. In both cases, the driver feedback was that the car starts to oversteer while braking into the corner. This is, of course, a very uncomfortable situation when braking into the corner. In the GT3 project, we just increased the preload of the diff, and the problem was gone. In the other project, we increased preload and changed diff ramps.
Full scale vs. 1/8 scale racing
So, if we compare full scale racing with small scale racing, what is the conclusion? The application is the same, and you want to adjust the diff using the same principle. When the car gets nervous/fish tailing in an off power situation, you want to increase the oil density in RC racing or increase preload (change ramps, the cooling aspect also plays a major role when you change oil) in full scale racing, so you reduce the wheel speed difference between the left and right tires.
I hope this article will help some people to know a little more about differentials. For myself, you could even call it a sort of technical diary because when I write things down, they stay in my head a little better, sometimes. In case you have further questions, send me a message and I will ask an expert. 😊